Napędy LNG
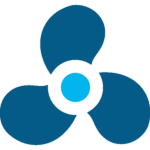
Od czego zależy dobór napędu statku LNG
Dobór napędu statku uwarunkowany jest względami ekonomicznymi (proporcją cen, efektywnością, kosztami serwisu), dostępnością paliwa, niezawodnością, trwałością oraz przepisami chroniącymi środowisko.
Choć wydawałoby się, że na statkach LNG paliwa w postaci gazu jest pod dostatkiem, to jego wykorzystanie do napędu i wytwarzania prądu nie było takie oczywiste. W przeszłości, przy taniej ropie naftowej w stosunku do gazu, oraz braku ograniczeń środowiskowych, opłacało się konstruować statki z napędem klasycznym, na mazut (paliwo ciężkie) i diesel (paliwo lekkie). W celu utrzymania niskiego ciśnienia w zbiornikach parujący gaz ponownie skraplano, co wymagało dużego nakładu energetycznego również pozyskiwanego ze spalania ropy.
Z czasem przepisy zaostrzano, szczególnie ograniczając spalanie ciężkich frakcji ropy z dodatkiem siarki. Również stosunek ceny ropy do gazu zaczął się odwracać. Wykorzystanie gazu zaczęło się bardziej opłacać, unikając zarazem kosztów jego ponownego skraplania.
Przy obecnych przepisach chroniących środowisko i ograniczających emisję szkodliwych substancji do powietrza, oraz przy rosnących kosztach transportu morskiego, nacisk kładzie się na efektywność zarówno napędów jak i izolacji zbiorników ograniczających parowanie. W ten sposób minimalizuje się zarówno potrzebę ponownego skraplania jak i zużycie paliwa w jednostce napędowej. Ważne są również koszty i okresy pomiędzy między serwisami.
Doświadczenie pokazało również, że warto mieć możliwość zmiany paliwa w zależności od aktualnej sytuacji na rynku.
Rodzaje napędów stosowanych na statkach LNG
Na statkach LNG można wykorzystać następujące typy układów napędowych:
- CST – Konwencjonalna turbina parowa konwencjonalna , zasilana gazem lub olejem napędowym (LNG, HFO, MDO).
- AST – Zaawansowana turbina parowa (z dogrzewaniem, odzyskiem lub łączona z innym silnikiem) zasilana gazem lub olejem napędowym (LNG, HFO, MDO).
- COGAS – Kombinowana turbina gazowo parowa zasilana gazem lub olejem napędowym (LNG, HFO, MDO).
- COGES – Kombinowana turbina gazowo elektryczno parowa zasilana gazem lub olejem napędowym (LNG, HFO, MDO).
- DRL – Wolnoobrotowy silnik wysokoprężny zasilany tylko olejem napędowym (HFO, MDO) z systemem skraplania gazu.
- DFDE – Wolnoobrotowy dwupaliwowy silnik diesel-elektryczny zasilany gazem lub paliwem lekkim (LNG, MDO).
- TFDE – Wolnoobrotowy trzypaliwowy silnik diesel-elektryczny zasilany gazem, paliwem ciężkim lub paliwem lekkim (LNG, HFO, MDO).
- MEGI – Wolnoobrotowy silnik wysokoprężny z wtryskiem gazu pod wysokim ciśnieniem zasilany gazem, paliwem ciekłym lub mieszanką (LNG, HFO, MDO).
- XDF- Wolnoobrotowy silnik wysokoprężny z wtryskiem gazu pod niskim ciśnieniem zasilany gazem, paliwem ciekłym lub mieszanką (LNG, HFO, MDO).
Efektywność napędów stosowanych na statkach LNG
Efektywność napędu zależy nie tylko od jego typu, ale i zaawansowania technologicznego konkretnego rozwiązania. Ciężko jest porównywać model z roku 1962 z modelem z roku 2020. Nowoczesna turbina może być bardziej efektywna od starszych silników wysokoprężnych. Producenci rywalizują ze sobą ulepszając swoje konstrukcje i z każdym nowym rozwiązaniem efektywność jest podnoszona.
Trzeba też pamiętać, że całkowita sprawność zależy od indywidualnej sprawności poszczególnych elementów systemu napędowego (turbiny, silniki spalinowe, silniki elektryczne, wały napędowe, przekładnie, przetwornice, transformatory, rozdzielnice, alternatory). Są one rozwijane oddzielnie, często przez wielu różnych producentów i łączone na potrzeby konkretnej jednostki.
Podobnie jest ze współczynnikami ekologicznymi. Emisja gazów spada wraz z podnoszeniem sprawności oraz wprowadzaniem nowych patentów. W niektórych silnikach spalanie gazu musi być inicjowane wcześniejszym spalaniem oleju, jednak są i systemy bezpośredniego zapłonu iskrowego gazu, co do nie dawna było zabronione ze względów bezpieczeństwa. Niektóre silniki mogą przejść na spalanie gazu tylko po osiągnięciu odpowiedniego obciążenia i może się ono znacznie różnić pomiędzy modelami i producentami. Emisja tlenków siarki zależy od zawartości siarki w paliwie, która jest zmniejszana wraz z wprowadzaniem nowych norm.
Poniższą tabelę należy więc traktować jedynie orientacyjnie.
Rodzaj napędu | Sprawność napędu | Emisja NOx | Emisja SOx | Emisja CO2 |
---|---|---|---|---|
Turbina parowa konwencjolanlna | 30.6% | 1 g/kWh | 11 g/kWh | 900 g/kWh |
Turbina ultra parowa | 41.1% | 1 g/kWh | 0 g/kWh | 500 g/kWh |
Turbina gazowa w cyklu kombinowanym | 41.1% | 2.5 g/kWh | 0 g/kWh | 480 g/kWh |
Wolnoobrotowy silnik wysokoprężny konwencjonalny | 47.5% | 17 g/kWh | 7.7 g/kWh | 580 g/kWh |
Wolnoobrotowy dwu/trzy paliwowy silnik diesel-elektryczny | 42.0% | 1.3 g/kWh | 0.5 g/kWh | 480 g/kWh |
Wolnoobrotowy silnik wysokoprężny z bezpośrednim wtryskiem gazu | 51.2% | 10.1 g/kWh | 0.88 g/kWh | 446 g/kWh |
Opis napędów statków LNG
Turbina parowa
Pracuje zgodnie z cyklem Clausiu’s-Rankine’a.
Obieg ten składa się z następujących przemian:
1 – 2 – izentropowego (adiabatycznego) rozprężania pary w turbinie parowej,
2 – 3 – izobarycznego skroplenia rozprężonej pary (odprowadzenia ciepła w skraplaczu),
3 – 4 – izochorycznego pompowania kondensatu w pompie,
4 – 1 – izobarycznego podgrzewania cieczy (wody), jej odparowania oraz przegrzewania powstałej pary w kotle parowym lub wytwornicy pary.
- CST (Conventional Steam Turbine) – Konwencjonalna Turbina Parowa
Gaz parujący w zbiornikach ładunkowych (BOG) jest pobierany przez sprężarkę o niskim obciążeniu (LD) i doprowadzany do kotła, gdzie jest spalany. Energia termiczna, wytworzona podczas spalania, podgrzewa wodę do stanu pary przegrzanej o ciśnieniu 60 barów i temperaturze 520ºC, która napędza turbinę wysoko i niskoprężną. Ta z kolei, poprzez przekładnię redukcyjną (zmniejszającą prędkość obrotową z 6000 RPM do 80 RMP), napędza poprzez wał śrubę. Para natomiast jest ponownie skraplana i wraca do kotła.
Z pary korzystają również turbogeneratory wytwarzające prąd.
Z reguły stosuje się dwa kotły i dwa turbogeneratory. Awaryjnie montuje się klasyczne czterosuwowe generatory wysokoprężne na olej napędowy.
W kotle można spalać zarówno gaz jak i olej napędowy zarówno ciężki jak i lekki lub mieszankę paliw w dowolnych proporcjach.
Nadmiar parującego gazu można spalić w kotle, a niewykorzystane ciepło zrzucić do skraplacza chłodzonego wodą morską. Niedobór natomiast można zaspokoić wymuszeniem parowania gazu lub dowolnym innym paliwem.
Zalety turbin: proste w konstrukcji, niezawodne, trwałe, nie wymagają konserwacji, nieskomplikowane w obsłudze, elastyczne w spalaniu dowolnego paliwa, mogą zużyć nadmiar parującego gazu bez dodatkowych instalacji.
Wady turbin: niska sprawność całkowita (szczególnie w generatorach prądu oraz przy niskich obciążeniach), duża konsumpcja paliwa, niskie wskaźniki ekologiczne (wysoka emisja CO2), wymagają dużo przestrzeni, o 40% zmniejszona moc podczas pracy wstecz, wydłużony czas odpowiedzi na zmianę kierunku obrotu śruby napędowej, możliwość wystąpienia korozji jeśli para jest niewystarczająco sucha i skrapla się w turbinie.
- RSP (Reheat Steam Turbine Plant), ART (Advanced Reheat Turbine), UST (Ultra Steam Turbine), STAGE (Steam Turbine and Gas Engine) – Zaawansowane turbiny parowe z dogrzewaniem par, odzyskiem ciepła oraz łączone z silnikami wysokoprężnymi.
Ze względu na największą wadę klasycznych turbin parowych, czyli jej efektywność, trwają prace nad modyfikacją parametrów pary i odzyskiem ciepła.
Jedną z koncepcji jest dogrzewanie pary. Po przejściu przez turbinę wysokoprężną, część pary wraca do dodatkowej nagrzewnicy w kotle, a następnie jest kierowana na turbinę średnioprężną a po niej na niskoprężną, potem na skraplacz i wraca do kotła. Pozwala to na zwiększenie średniej temperatury przekazywania ciepła do czynnika w obiegu, co zwiększa sprawność. Powoduje to też zwiększenie stopnia suchości pary na ostatnich stopniach turbiny (opóźnienie kondensacji), co ma korzystny wpływ na żywotność turbiny zmniejszając erozję jej łopatek.
Kolejną metodą jest odzyskiwanie ciepła skraplania w nagrzewnicy regeneracyjnej. Bez niej ciepło to byłoby wyrzucone do otoczenia i stracone dla układu. Regeneracyjny podgrzew wody zasilającej kocioł realizowany jest zwykle w kilku wymiennikach, dzięki czemu minimalizowane są straty. Część wymienników umieszczona jest przed pompą zasilającą (wymienniki niskoprężne), a część za (wymienniki wysokoprężne). Przynosi to zwiększenie sprawności o kilka do kilkunastu procent, ale zwiększa stopień komplikacji i cenę systemu.
Następnym rozwiązaniem jest połączenie silnika wysokoprężnego z turbiną. Zastosowano w nim dwie śruby. Jedna jest napędzana turbiną parową a druga silnikiem elektrycznym zasilanym przez dwu/trzy paliwowy silnik wysokoprężny. W takim systemie ciepło odpadowe silnika wysokoprężnego jest wykorzystywane w nagrzewnicach wody zasilającej kocioł. Pozwala to zwiększyć sprawność termiczną o 20% w stosunku do klasycznej turbiny.
Natomiast aby rozwiązać problem mniejszej sprawności turbiny przy małych obciążeniach, zamiast jednego dużego układu stosuje się dwa mniejsze, niezależne od siebie. Może też być jedna mniejsza turbina parowa, zaspokajająca zapotrzebowanie statku podczas operacji w porcie, a druga większa, zaspokajająca zapotrzebowanie podczas podróży z pełną prędkością morską. Daje to nie tylko możliwość wyłączenie jednego systemu przy spadku obciążenia ale i zapewnia redundancję.
Turbina gazowa
Pracuje zgodnie z cyklem Braytona-Joule’a.
Obieg ten składa się z następujących przemian:
1-2 – sprężanie adiabatyczne,
2-3 – izobaryczne dostarczenie ciepła (spalanie wewnętrzne paliwa),
3-4 – rozprężanie adiabatyczne,
4-1 – izobaryczne chłodzenie (wydalenie gorącego czynnika po rozprężeniu w turbinie i zassanie zimnego powietrza z otoczenia).
W turbinach gazowych zamiast systemu pary wodnej wykorzystuje się gazy wylotowe, które napędzają turbiny. Nie są to systemy jeszcze stosowane na statkach LNG, ale występują na promach pasażerskich. Mogą być zasilane dowolnym paliwem, w tym gazem, więc nic nie stoi na przeszkodzie w ich wykorzystaniu na tym typie jednostek. Pewną blokadą jest cena systemu kombinowanego, oraz to, że podczas spalania gazu występują większe temperatury, które przyspieszają zużycie materiałów.
Aby zwiększyć efektywność turbin gazowych, mogą występować kombinacje z parą, odzyskiem ciepła, dogrzewaniem, czy wykorzystaniem pary do innych celów. Każdy z nich ma nieco inne zalety i wady, ale generalnie turbiny gazowe są wydajniejsze od parowych. Sprawdzają się szczególnie przy większych obciążeniach i dłuższych przelotach pomiędzy portami. Zajmują też mniej miejsca i są lżejsze. Do tego ich trwałość jest duża, a koszty konserwacji niskie.
W efektywniejszych turbinach kombinowanych dochodzi jeszcze układ parowy. Podnosi on efektywność układu o 15-20% bez zwiększenia zużycia paliwa. Wymaga jednak dodatkowej instalacji a jej efektywność zależy od ilości rur w nagrzewnicy, co zajmuje i przestrzeń i zwiększa masę.
Strona gazowa składa się z kotła, w którym spalane jest paliwo, mieszane ze sprężonym powietrzem dostarczanym za pomocą sprężarki, oraz turbiny wielostopniowej zasilającej sprężarkę powietrza wlotowego, napędy mechaniczne (wał śruby) i generatory prądu. W przegrzewaczu gazy wylotowe dogrzewają też parę wodną, wstępnie ogrzaną w ekonomizerze i kotle.
Strona parowa składa się z systemu jej wytwarzania; ekonomizera, sekcji kotła, przegrzewacza. A następnie z odbiorników czyli z turbiny parowej. Później z wykraplacza, pomp i zbiornika odpowietrzającego.
Turbina parowa, lub energia cieplna pary, może być wykorzystana na kilka sposobów:
- COGAS – Kombinowana turbina gazowo parowa.
W niej para wykorzystana jest, poprzez turbinę parową, do zasilania napędów mechanicznych.
- COGES – Kombinowana turbina gazowo elektryczno parowa.
W której para wykorzystana jest, poprzez turbinę parową, do zasilania generatorów prądu
- COGEN – Kombinowana turbina gazowo parowo energetyczna.
Gdzie energia cieplna pary wykorzystana jest bezpośrednio przez innych odbiorców ciepła jak na przykład generatory wody słodkiej.
Dwucylindrowy wolnoobrotowy silnik wysokoprężny
Pracuje zgodnie z cyklem Seiligera-Sabathé:
Obieg ten składa się z następujących przemian:
1-2 adiabatyczne sprężanie,
2-3 izochoryczne podgrzewanie czynnika,
3-4 izobaryczne podgrzewanie czynnika,
4-5 adiabatyczne rozprężanie,
5-1 izochoryczne oziębianie czynnika.
Silnik spalinowy z samozapłonem, bez gaźnika i iskry inicjującej. Paliwo pod ciśnieniem wtryskiwane jest poprzez dysze rozpylające do komory spalania wypełnionej wcześniej sprężonym, gorącym powietrzem. Po samozapłonie gwałtownie rośnie temperatura i następuje ekspansja czynnika roboczego oraz wykonanie pracy suwu tłoka. Ciśnienie, które początkowo wzrosło spada, ale dzięki dopalaniu mieszanki paliwa i powietrza, utrzymuje się na stałym poziomie.
Jest to klasyczny silnik używany na wszystkich typach statków. Napęd jest bezpośrednio połączony z wałem śruby. Są one znane i wykorzystywane od lat, przez co są dopracowane, trwałe, nie są zbyt drogie w zakupie i utrzymaniu. Istnieje też duża liczba wykwalifikowanych mechaników zaznajomionych z takim rozwiązaniem. Silniki wysokoprężne mają wysoką sprawność i mogą spalać dowolny olej napędowy (HFO, MDO), również ten o słabej jakości.
Jego wadą w zastosowaniu na statkach LNG jest jednak to, że nie wykorzystuje on gazu odparowującego w zbiornikach. Dlatego statki LNG, wyposażone w klasyczny silnik wysokoprężny, muszą posiadać system kontrolowanego spalania gazu (GCU) i system skraplania gazu. Ze względu na bardzo niską temperaturę LNG taki układ jest skomplikowany i energochłonny. Rzeczywista efektywność, z uwzględnieniem potrzeby skraplania, jest więc mocno obniżona. Kolejną jego wadą jest duża emisja szkodliwych związków.
W skład pełnego układu wchodzą również generatory prądu, a jego zużycie przez systemy ładunkowe jest duże. Z reguły są to czterocylindrowe silniki wysokoprężne.
W czasach gdy normy ochrony środowiska nie były tak surowe jak obecnie, a cena ropy naftowej, w stosunku do gazu, była niska, powstało sporo statków LNG z takim rozwiązaniem.
Obecnie nie buduje się statków z klasycznym napędem wysokoprężnym i systemem skraplania gazu LNG.
Wielopaliwowy, wolnoobrotowy napęd diesel-elektryczny
Pracuje zgodnie z cyklem Otto:
Obieg ten składa się z następujących przemian:
1-2 sprężanie adiabatyczne,
2-3 ogrzewanie izochoryczne (wskutek spalania mieszanki paliwowej, silnik spalinowy),
3-4 rozprężanie adiabatyczne,
4-1 chłodzenie izochoryczne – wydech,
1-0-1 wtrysk paliwa i zasysanie mieszanki.
Prąd, wykorzystywany przez silniki elektryczne, oraz inne odbiorniki, wytwarzany jest przez czterosuwowe, średnioobrotowe generatory wysokoprężne, które mogą być dwupaliwowe (LNG, MDO), lub trzypaliwowe (LNG, HFO, MDO). Na początku ich produkcji występowały głównie dwupaliwowe. Później system zmodyfikowano umożliwiając spalanie i paliwa ciężkiego.
Gaz wtryskiwany jest do powietrza dolotowego za pomocą zaworu wlotowego. Czas jego otwarcia decyduje o dawce paliwa. Spalanie inicjowane jest zapłonem paliwa lekkiego, które wtryskiwane jest poprzez zawory pilotowe. Generatory te nie mogą więc działać bez potrzeby zużywania MDO.
Generatory czterosuwowe mają wysoką sprawność oraz mogą być umieszczone w dowolnym miejscu, co ułatwia organizację siłowni. Do tego w systemie wykorzystywane są bardzo wysokie napięcia ok. 6600V, co dodatkowo ogranicza straty i zwiększa wydajność systemu.
Mają jednak i swoje wady.
Jedną z nich jest stukanie do którego dochodzi gdy szczyt procesu spalania nie występuje w optymalnym momencie. Następuje wtedy niekontrolowane uwolnienie energii i rozchodzenie się fal ciśnienia w komorze spalania. Te fale ciśnienia mogą powodować rezonans komory spalania z naturalną częstotliwością, co skutkuje typowym słyszalnym dźwiękiem znanym jako „stukanie”. Zwiększa się ono gdy w gazie odparowującym ze zbiornika zwiększa się ilość cięższych komponentów (etan, propan), które mają inny stopień sprężania, wyższą wartość energetyczną oraz niższą temperaturę zapłonu. Wówczas silniki te nie mogą pracować z pełną mocą, a po przekroczeniu wartości krytycznych, automatycznie przechodzą w tryb spalania tylko oleju napędowego.
Do tego, poza generatorami prądu, do napędu statku potrzebne są jeszcze; tablica rozdzielcza wysokiego napięcia, transformator, przetwornica częstotliwości, elektryczny silnik napędowy, przekładnia i wał napędowy. Znacznie to komplikuje system i zwiększa zarówno jego cenę początkową jak i cenę późniejszych przeglądów i napraw. Stwarza też potencjalnie więcej problemów eksploatacyjnych.
Przy mniejszych prędkościach statku zużycie gazu w generatorach prądu może nie być wystarczające, więc wymagane jest zainstalowanie albo systemu kontrolowanego spalania (GCU), albo systemu częściowego lub całkowitego skraplania parującego gazu.
Wolnoobrotowy, dwusuwowy silnik wysokoprężny z bezpośrednim wtryskiem gazu pod wysokim ciśnieniem (ME-GI)
Pracuje zgodnie z cyklem Seiligera-Sabathé:
Obieg ten składa się z następujących przemian:
1-2 adiabatyczne sprężanie,
2-3 izochoryczne podgrzewanie czynnika,
3-4 izobaryczne podgrzewanie czynnika,
4-5 adiabatyczne rozprężanie,
5-1 izochoryczne oziębianie czynnika.
Jest to silnik dwusuwowy, pracujący na podobnej zasadzie jak klasyczny, tylko przystosowany do spalania gazu lub mieszanki gazu z olejem napędowym w dowolnej proporcji (LNG, HFO, MDO).
Parujący ze zbiorników ładunkowych gaz jest sprężany do bardzo wysokiego ciśnienia, 250-300 bar, dostarczany do siłowni i wtryskiwany bezpośrednio do cylindra, blisko jego górnego położenia, już po zapłonie paliwa pilotowego, którym może być MDO lub HFO.
Gaz nie bierze więc udziału w sprężaniu co eliminuje stukanie. Taki silnik może więc spalać paliwo o dowolnym składzie gazowym lub mieszankę gazu i oleju napędowego lub sam olej napędowy.
Ma do tego wysoką wydajność energetyczną i umożliwia bezpośrednie podłączenie do wału napędowego. Silniki są również bardziej ekologiczne od klasycznych napędów dwusuwowych.
Jednak i one mają swoje wady.
Jedną z nich jest potrzeba zastosowania systemu wysokociśnieniowego. Ciśnienie gazu jest osiągane albo poprzez użycie sprężarki tłokowej, albo poprzez użycie wyparownika (LNG w temperaturze otoczenia osiąga ok 300 bar). Potrzebne są też specjalne, wytrzymałe rury złożone z dwóch warstw. Przestrzeń pomiędzy tymi warstwami wyposażona jest w mechaniczną wentylację podciśnieniową usuwającą gaz w przypadku nieszczelności. Dzięki temu siłownia okrętowa nie jest traktowana jako wysokociśnieniowa w myśl przepisów klasyfikacyjnych. Materiały i system ochronny są jednak drogie a układ wciąż uważany za potencjalnie niebezpieczny.
Kolejną wadą jest zbyt wysoka emisja spalin aby spełniać najnowsze normy ochrony środowiska. Wymagane jest więc zastosowanie systemu oczyszczania z selektywną katalityczną redukcją (SCR) lub ulepszonej recyrkulacji spalin (EGR). Również przejście na spalanie gazu w silniku może nastąpić dopiero po osiągnięciu odpowiedniego obciążenia, które jest znacznie większe niż w przypadku czterosuwowych silników wielopaliwowych.
Silniki MEGI potrzebują też około 0.5-8% oleju napędowego, nawet przy pracy na gazie.
Przy pracy na gazie obciążenie silnika nie może spaść poniżej 10%.
W przypadku mniejszego zapotrzebowania na moc prędkość odparowywania gazu może przekroczyć jego zużycie, więc statki z takim napędem posiadają również system kontrolowanego spalania gazu (GCU). Mogą też posiadać częściowy lub całkowity system skraplania gazu.
A a by zwiększyć elastyczność pracy, zapewnić redundancję i zmniejszyć wielkość silnika często stosuje się dwa silniki, każdy napędzający inną śrubę.
Wolnoobrotowy silnik wysokoprężny z bezpośrednim wtryskiem gazu pod niskim ciśnieniem (X-DF)
Pracuje zgodnie z cyklem Otto:
Obieg ten składa się z następujących przemian:
1-2 sprężanie adiabatyczne,
2-3 ogrzewanie izochoryczne (wskutek spalania mieszanki paliwowej, silnik spalinowy),
3-4 rozprężanie adiabatyczne,
4-1 chłodzenie izochoryczne – wydech,
1-0-1 wtrysk paliwa i zasysanie mieszanki.
Jest to wolnoobrotowy silnik wysokoprężny przystosowany do spalania gazu lub mieszanki gazu z olejem napędowym w dowolnej proporcji (LNG, HFO, MDO).
Parujący ze zbiorników ładunkowych gaz jest sprężany do ciśnienia, 10-15 bar, dostarczany do siłowni i wtryskiwany bezpośrednio do cylindra, w okolicach jego środkowego położenia. Gaz jest dobrze mieszany z powietrzem przed nastąpieniem zapłonu, a mieszanina jest uboga. To pozwala obniżyć temperatury spalania i zmniejszyć emisje NOx. Spalanie musi być zainicjowane wcześniejszym zapłonem oleju napędowego, wtryskiwanego poprzez zawory pilotowe, podobnie jak w przypadku silników TFDE.
Silnik ten spełnia normy ekologiczne bez potrzeby stosowania dodatkowych systemów SCR i EGR.
Do zasilania gazu stosuje się dobrze znane, trwałe i stosowane od lat sprężarki niskoprężne oraz rury doprowadzające wykonane ze standardowych materiałów. System jest więc prostszy w konstrukcji, tańszy i bezpieczniejszy.
Silniki mają wysoką wydajność energetyczną i umożliwia bezpośrednie podłączenie do wału napędowego.
Całkowite zużycie oleju napędowego do zaworów pilotowych wynosi ok. 0.5% – 1%, jest więc mniejsze niż w systemie MEGI.
Silniki XDF mogą też pracować na gazie nawet przy 5% obciążeniu, podczas gdy MEGI powyżej 10%, a przełączenia na gaz można dokonać przy obciążeniach w zakresie 10-80%.
Dzięki ubogiej mieszance gaz-powietrze, oraz niskiej temperaturze powietrza silniki X-DF nie mają wady silników TFDE i nie występuje w nich stukanie.
W stosunku do systemu wysokociśnieniowego, silniki niskociśnieniowe mają nieco mniejszą sprawność, około 3% na gazie i 9% na oleju napędowym.
W przypadku mniejszego zapotrzebowania na moc prędkość odparowywania gazu może przekroczyć jego zużycie, więc statki z takim napędem posiadają również system kontrolowanego spalania gazu (GCU). Mogą też posiadać częściowy lub całkowity system skraplania gazu.