LNG - Konstrukcja
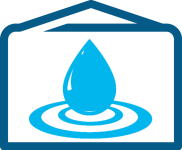
Kody regulujące konstrukcję gazowców
GC Code – kod budowy i wyposażenia statków przewożących luzem skroplone gazy
Pierwszy kod regulujący budowę gazowców, przyjęty w listopadzie 1975 i dotyczący statków zamówionych po październiku 1976 lub dostarczonych po czerwcu 1980.
Regulował on przewóz 27 gazów skroplonych i innych substancji oraz definiował gaz skroplony jako produkt którego bezwzględna prężność par przekracza 2.8 kPa/cm2 w temperaturze 37.8°C. Do listy dodano kilka wyjątków które nie spełniały tego kryterium jak chlor czy tlenek etylenu.
IGC Code – międzynarodowy kod dotyczący budowy i wyposażenia statków przewożących luzem skroplone gazy
Jest on rozwinięciem kodu GC. Stał się obowiązkowy od lipca 1986.
Kod jest ciągle poprawiany na podstawie analizy wypadków, czy też zmian w dostępnych technologiach. Statki muszą być zgodne z tą wersją kodu, która była aktualna podczas jego konstruowania.
W stosunku do GC kodu dodatkowo reguluje konstrukcję, materiały i lokalizację zbiorników ładunkowych i innych zbiorników ciśnieniowych, rurociągów oraz zdolności statku do przetrwania w celu zminimalizowania wycieku ładunku podczas wypadku.
Wynikają z niego typy możliwych konstrukcji gazowców.
Standardy konstrukcji gazowców
Statki zbudowane zgodnie z kodem IGC muszą spełniać wymagania konstrukcyjne dla jednego z poniższych standardów:
- Typ 1G – dla zbiornikowców, które zamierzają przewozić ładunki wymienione w kodzie IGC i których przewóz wymaga maksymalnych środków zapobiegania wyciekom jak na przykład chlor czy dwutlenek siarki.
- Typ 2G – dla zbiornikowców, które zamierzają przewozić ładunki wymienione w kodzie IGC i których przewóz wymaga znaczących środków zapobiegania wyciekom jak na przykład amoniak, metan, propan, butan.
- Typ 2PG – dla zbiornikowców, które zamierzają przewozić ładunki wymienione w kodzie IGC i których przewóz wymaga znaczących środków zapobiegania wyciekom jak na przykład amoniak, metan, propan butan.
Długość tych statków nie może być większa niż 150m, zbiorniki muszą być niezależne typu C, dopuszczalna temperatura zbiorników wynosi -55°C lub więcej (cieplej), a nastawa zaworu bezpieczeństwa (MARVS) wynosi przynajmniej 7 barów.
- Typ 3G – dla zbiornikowców, które zamierzają przewozić ładunki wymienione w kodzie IGC i których przewóz wymaga średnich środków zapobiegania wyciekom jak na przykład azot czy dwutlenek węgla.
Typy gazowców według ciśnienia
Statki służące do przewozu gazów skroplonych można też podzielić ze względu na ciśnienie i temperaturę przewożonego ładunku:
- Pełno ciśnieniowe – przewożą ładunek w temperaturze otoczenia, pod wysokim ciśnieniem. Minimalna dozwolona temperatura to zwykle -10°C, ale można spotkać i statki z limitem do -24°C. Ciśnienia robocze dochodzą do 18 barów. Zbiorniki są cylindryczne lub kuliste, niezależne, samonośne. Wykonane z normalnej stali. Statki pełno ciśnieniowe nie mają systemów chłodzących ani izolacji zbiorników. Nie muszą mieć bariery wtórnej ani przestrzeni dookoła zbiornika wypełnionych gazem obojętnym. Nie mają też pomp. Wyładunek odbywa się poprzez wypychanie cieczy przez ciśnienie gazu pobieranego z innych zbiorników i wpompowywanego poprzez kompresor do wyładowywanego zbiornika. Na linii wyładunkowej może być zainstalowana pompa wspomagająca i zwiększająca ciśnienie, która przyspiesza operację.
Zalety: prosta konstrukcja, łatwa obsługa, brak systemów chłodzenia i pomp wyładunkowych, brak izolacji, możliwość użycia zwykłej stali, brak barier wtórnych.
Wady: duże niewykorzystane przestrzenie, duża grubość zbiorników i ciężar konstrukcji, ograniczona wielkość zbiorników (im większa tym zbiornik musi być grubszy), mała ekonomia przewozu.
Wykorzystanie: do przewozu ładunków LPG przeważnie na krótkich trasach.
- Średnio ciśnieniowe – przewożą ładunek schłodzony lub średnio schłodzony, pod średnim ciśnieniem. Minimalna dozwolona temperatura to -104°C dla etylenu, ale można spotkać i statki z limitem do -48°C do przewozu klasycznych ładunków LPG. Ciśnienia robocze dochodzą do 5-7 barów. Zbiorniki są cylindryczne, sferyczne lub dwu-cylindryczne (bi-lobe). Są niezależne, samonośne. Wykonane ze stali odpornej na żądaną temperaturę; stal nierdzewna lub z domieszką 5% niklu dla etylenu, albo drobnoziarnista stal węglowo-manganowa dla ładunków LPG. Statki średnio ciśnieniowe mają systemy skraplające pary ładunku oraz grubą izolację zbiorników. Nie muszą mieć bariery wtórnej ani przestrzeni dookoła zbiornika wypełnionych gazem obojętnym. Mają pompy wyładunkowe. Na linii wyładunkowej może być zainstalowana pompa wspomagająca, zwiększająca ciśnienie, która umożliwia wyładunek przeciwko wysokiemu ciśnieniu zwrotnemu. Mogą też posiadać system ogrzewania ładunku. Dzięki temu statki średnio ciśnieniowe mogą wyładowywać się zarówno na terminalach przystosowanych do ładunków pod ciśnieniem jak i w pełni schłodzonych. Mogą też izolować od siebie poszczególne zbiorniki i systemy skraplania i przewozić kilka różnych ładunków jednocześnie. Daje to ogromną elastyczność wykorzystania.
Zalety: konstrukcja nie jest zbyt skomplikowana, brak barier wtórnych, duża elastyczność i zakres możliwych temperatur i ciśnień, możliwości chłodzenia lub ogrzewania ładunku, dwukrotnie lepszy współczynnik ciężaru zbiorników do ciężaru przewożonego w nim gazu skroplonego niż w przypadku statków pełno ciśnieniowych.
Wady: wciąż spore niewykorzystane przestrzenie, zbiorniki cięższe i ekonomia przewozu gorsza niż statków w pełni schłodzonych, wymagają specjalistycznej wiedzy przy obsłudze urządzeń ładunkowych.
Wykorzystanie: do przewozu dowolnych ładunków LPG.
- W pełni schłodzone – przewożą ładunek schłodzony, pod ciśnieniem zbliżonym do atmosferycznego. Przyjęło się używać tej nazwy raczej wyłącznie dla statków LPG w celu rozróżnienia od statków w pełni ciśnieniowych i średnio ciśnieniowych. Jednak wszystkie statki LNG też należą do tej grupy, gdyż ładunki LNG zawsze są utrzymywane w stanie schłodzenia. Minimalna dozwolona temperatura to -163°C dla LNG, lub -48°C dla LPG. Ciśnienia robocze to 0.25 bara, czasem do 0.7 bara. Zbiorniki są głównie pryzmatyczne. Wykonane ze stali odpornej na żądaną temperaturę; inwar lub aluminium dla LNG, lub drobnoziarnista stal węglowo-manganowa dla LPG. Statki w pełni schłodzone muszą utrzymać ładunek pod bardzo niskim ciśnieniem albo za pomocą systemów skraplania par gazów, albo poprzez ich zużycie do napędu statku lub kontrolowane spalenie. Muszą mieć bariery wtórne. Przestrzeń pomiędzy barierami wypełniona jest gazem obojętnym. Mają po dwie pompy wyładunkowe na jeden zbiornik, gdyż nie ma możliwości zbudowania ciśnienia w celu wypchnięcia ładunku w przypadku ich awarii. Na linii wyładunkowej statków LPG montuje się pompy wspomagające, zwiększająca ciśnienie oraz wymiennik ciepła mogący ogrzewać ładunek. Na LNG takiej potrzeby nie ma.
Zalety: najlepsze wykorzystanie przestrzeni statku i współczynnik ekonomi przewozu ładunku, lekkie, dobrze izolowane zbiorniki
Wady: wymagają sprawnych urządzeń skraplających parujący gaz lub wykorzystujących go do napędu oraz specjalistycznej wiedzy przy obsłudze tych urządzeń.
Wykorzystanie: do przewozu w pełni schłodzonych ładunków LNG i LPG.
Systemy przechowywania ładunku
Zbiorniki można podzielić na następujące typy konstrukcyjne:
- Integralne – zbiorniki stanowią konstrukcyjną część kadłuba statku. Przez to podlegają takim samym obciążeniom, które obciążają sąsiednią konstrukcję kadłuba.
Są dopuszczalne dla ładunków o temperaturze wrzenia do -10°C a dopuszczalne ciśnienie wynosi 0.25 bara.
Zalety: największa przestrzeń ładunkowa, brak barier.
Wady: brak miejsca na izolację, ograniczenia dopuszczalnego ciśnienia i temperatury.
Wykorzystanie: do przewozu butanu, ale przeważnie niestosowane. Praktycznie niespotykane.
- Membranowe – zbiorniki składają się z cienkiej warstwy, membrany, podpartej sąsiadującą konstrukcją kadłuba poprzez izolację. Nie są samonośne. Membrana jest zaprojektowana w taki sposób, by była cieczo i gazoszczelna a jej termiczna rozszerzalność i kurczliwość nie powodowała nadmiernych naprężeń.
Są dopuszczalne dla wszystkich ładunków niezależnie od temperatury wrzenia. Jednak gdy jest ona poniżej -10°C wymagana jest bariera wtórna. Dopuszczalne ciśnienie wynosi 0.25 bara, ale w zależności od wytrzymałości konkretnej konstrukcji może być zwiększona do 0.7 bara.
Zalety: duża przestrzeń ładunkowa, duże doświadczenie w wykorzystaniu na statkach, izolacja ograniczająca parowanie, lekkość konstrukcji, materiały wytrzymujące bardzo niskie temperatury.
Wady: ograniczona odporność na uszkodzenia, duże swobodne powierzchnie cieczy i efekt przemieszczania cieczy i uderzania jej o membranę (sloshing effect), ograniczenie możliwych stanów załadowania zbiornika (z reguły zabronione stany to pomiędzy 10% a 70%), ograniczenia dopuszczalnego ciśnienia i potrzeba utrzymywania ładunku w stanie pełnego schłodzenia, wymagana bariera wtórna.
Wykorzystanie: stosuje się do przewozu LNG.
- Pół-membranowe – zbiorniki składają się częściowo z cienkiej warstwy, membrany, podpartej sąsiadującą konstrukcją kadłuba poprzez izolację, a częściowo z części zaokrąglonych (na rogach zbiornika), przejmujących rozszerzenia termiczne. Są samonośne w stanie pustym, ale nie są samonośne gdy są załadowane. Wówczas ich góra, środek i spód muszą być podparte, poprzez izolację, sąsiadującą konstrukcją kadłuba.
Są dopuszczalne dla wszystkich ładunków niezależnie od temperatury wrzenia. Jednak gdy jest ona poniżej -10°C wymagana jest bariera wtórna.
Zalety: w porównaniu z pełną membraną mogą wytrzymywać większe ciśnienia i mieć mniejsze ograniczenia stanów załadowania zbiornika.
Wady: w porównaniu z pełną membraną są grubsze i cięższe oraz wymagają nieco większej przestrzeni na części zaokrąglone zbiornika, wymagają bariery wtórnej.
Wykorzystanie: w ograniczonym zakresie do przewozu ładunków LPG, choć zaprojektowane zostały dla statków LNG. Bardzo rzadko spotykana konstrukcja.
- Niezależne – zbiorniki nie stanowią części konstrukcji kadłuba. Są całkowicie samonośne zarówno jak są puste jak i w stanie załadowanym.
Zbiorniki niezależne dzieli się na trzy dodatkowe podtypy:
> Niezależne Typu A – Zaprojektowany przy użyciu klasycznej procedury analizy konstrukcyjnej. Zbiorniki przeważnie płaskie (pryzmatyczne) z wewnętrznym usztywnieniem dzięki czemu są samonośne. Przegroda środkowa dodatkowo zapobiega przemieszczaniu się ładunku.
Są dopuszczalne dla wszystkich ładunków niezależnie od temperatury wrzenia. Jednak gdy jest ona poniżej -10°C wymagana jest bariera wtórna. Do temperatury -55°C wtórną barierą może być kadłub, pod warunkiem, że jest on wykonany z odpowiednio wytrzymałego materiału.
Dopuszczalne ciśnienie wynosi do 0.7 bara.
Pomiędzy zbiornikiem a barierą wtórną (lub kadłubem) stosuje się izolację pianową lub z perlitu. Przestrzenie te wypełnione muszą być gazem obojętnym.
Zalety: duża przestrzeń ładunkowa, wytrzymałe, samonośne, z przegrodą ograniczającą efekt swobodnych powierzchni cieczy i uderzania cieczy o ściany konstrukcji (sloshing effect), mniejsze ograniczenia dozwolonych stanów załadowania.
Wady: wymagają więcej materiałów konstrukcyjnych na wzmocnienia wewnętrzne, cięższe, przewożony ładunek należy utrzymywać w stanie pełnego schłodzenia, wymagają bariery wtórnej.
Wykorzystanie: do przewozu ładunków LPG i LNG.
> Niezależne Typu B – Zaprojektowany przy użyciu testów modelowych, udoskonalonych narzędzi i metod analitycznych w celu określenia poziomu naprężeń, wytrzymałości zmęczeniowej i propagacji pęknięć.
Zbiorniki mogą być zarówno kuliste jak i płaskie (pryzmatyczne). Wykonane ze stali nierdzewnej lub aluminium. Wspierają się na drewnie lub wzmocnionych płytach ze sklejki.
Są dopuszczalne dla wszystkich ładunków niezależnie od temperatury wrzenia. Jednak gdy jest ona poniżej -10°C wymagana jest częściowa bariera wtórna.
Dopuszczalne ciśnienie wynosi do 0.7 bara dla zbiorników pryzmatycznych, dla zbiorników kulistych może być większa.
Na zewnątrz zbiornika stosuje się izolację, głównie pianową. Przestrzenie poza zbiornikiem nie muszą być wypełnione gazem obojętnym pod warunkiem takiej możliwości w przypadku wykrycia wycieku. bariera wtórna jest ograniczona tylko do dolnej części zbiornika.
Zalety: duża przestrzeń ładunkowa, zbiorników pryzmatycznych, wytrzymałe, samonośne, z przegrodą ograniczającą efekt swobodnych powierzchni cieczy i uderzania cieczy o ściany konstrukcji (sloshing effect), mniejsze ograniczenia dozwolonych stanów załadowania, zredukowana bariera wtórna.
Wady: gorzej wykorzystana przestrzeń ładunkowa przy zbiornikach kulistych, wymagają dokładnego projektowania i wykonania przez co niewiele stoczni może je robić, cięższe, przewożony ładunek należy utrzymywać w stanie pełnego schłodzenia.
Wykorzystanie: do przewozu ładunków LPG i LNG.
> Niezależne Typu C – Zaprojektowany zgodnie z normami konwencjonalnych zbiorników ciśnieniowych, dzięki czemu mogą być poddawane dokładnej analizie naprężeń. Naprężenia projektowe są utrzymywane na niskim poziomie.
Zbiorniki mogą być kuliste lub cylindryczne. Wykonane ze stali dostosowanej do temperatur przewożonego ładunku. Zbiorniki cylindryczne mogą być montowane na płasko lub w pionie.
Są dopuszczalne dla wszystkich ładunków i nie wymagają bariery wtórnej.
Dopuszczalne ciśnienie zależy od typu; mogą być to statki częściowo ciśnieniowe ok. 5 bar lub w pełni ciśnieniowe z ciśnieniem powyżej 7 bar.
Na zewnątrz zbiornika można stosować izolację minimalizującą ogrzewanie ładunku. Przestrzenie poza zbiornikiem nie muszą być wypełnione gazem obojętnym, mogą być wypełnione suchym powietrzem a nawet zwykłym powietrzem jeśli nie ma izolacji.
Zalety: wytrzymałe, samonośne, z przegrodą ograniczającą efekt swobodnych powierzchni cieczy i uderzania cieczy o ściany konstrukcji (sloshing effect), praktycznie brak ograniczenia dozwolonych stanów załadowania, brak bariery wtórnej, ładunku nie trzeba utrzymywać w stanie pełnego schłodzenia, tanie w budowie.
Wady: najgorzej wykorzystana przestrzeń ładunkowa i najgorsza ekonomia przewozu, ciężka stalowa konstrukcja.
Wykorzystanie: do przewozu ładunków LPG oraz etylenu i etanu.
Systemy izolacji zbiorników ładunkowych
Poza przewozem ładunków w pełni ciśnieniowych, wokół zbiorników stosuje się izolację, czasami podwójną; pomiędzy zbiornikiem i barierą wtórną i na zewnątrz bariery wtórnej.
Izolacja ma kluczowe znaczenie przy ograniczeniu przedostawania się ciepła z otoczenia do przewożonego ładunku a tym samym prędkości jego parowania i wysokości ciśnienia. Wymaga jednak przestrzeni, ma też swoją masę. Musi też przenosić naprężenia, więc jej dobór często jest uwarunkowany typem konstrukcji zbiornika.
Izolacja chroni również konstrukcję sąsiadującą ze zbiornikiem przed temperaturą, do której materiał może nie być przystosowany.
Izolacja nie należy do tanich, więc dobiera się ją również na podstawie potrzeb i planowanego wykorzystania statku. Im zimniejszy jest przewożony ładunek i mniejsze dozwolone ciśnienia robocze, tym ma większe znaczenie. Rata parowania, zależna właśnie od izolacji, determinuje również wydajność potrzebnych systemów skraplania, spalania lub zużycia ładunku do napędu.
Izolacja powinna mieć niską przewodność cieplną, niski ciężar, dużą wytrzymałość na uszkodzenia, dużą zdolność do przyjmowania obciążeń, być odporna na wilgoć, być kompatybilna z przewożonym ładunkiem w przypadku jego wycieku.
Materiały używane do izolacji zbiorników rozwijały się wraz z rozwojem technologii. Często są też ze sobą łączone; na przykład pomiędzy przestrzenie wzmacnianej sklejki daje się perlit lub na zewnątrz wełny folię aluminiową. Poniżej przedstawiamy kilka z nich:
- Drewno balsa – ogorzałka wełnista (Ochroma pyramidale) – rośnie w Ameryce Południowej. Jest niezwykle lekkie, nawet dwa razy lżejsze od korka. 1m3 balsy waży tylko 40kg. Jednocześnie jest mocne i sprężyste, a środek drewna jest bardzo miękki. Przewodność cieplna balsy wynosi 0.042-0.055 W/(m·K).
- Perlit ekspandowany – tlenek glinu krzemowego – jest skałą naturalną pochodzenia wulkanicznego. Powstał podczas szybkiego stygnięcia lawy, która zamykała we wnętrzu krople wody. Po wydobyciu jest mielony do osiągnięcia odpowiedniej granulacji i prażony dzięki czemu pęcznieje zwiększając objętość ponad dwudziestokrotnie. Jest lekki, niepalny, obojętny chemicznie, nieszkodliwy dla zdrowia. Służy do wypełniania całych przestrzeni wokół zbiornika lub przestrzeni skrzyń modułowych ze wzmacnianej sklejki. Przewodność cieplna perlitu wynosi 0.040-0.047 W/(m·K).
- Wełna mineralna skalna – jest pochodzenia mineralnego – otrzymywana w wyniku wytapiania skał bazaltu. Roztopiony surowiec poddaje się procesowi rozwłókniania, do otrzymanych włókien dodaje się lepiszcze. Może występować w postaci mat, płyt, otulin lub granulatu i może być łączona z innymi materiałami jak folia. Przewodność cieplna wełny mineralnej wynosi 0.035-0.045 W/(m·K).
- Wełna szklana – jest pochodzenia mineralnego – otrzymywana w wyniku topienia piasku kwarcowego (stłuczki szklanej) z dodatkiem skał gabro, dolomit lub wapień. Roztopiony surowiec poddaje się procesowi rozwłókniania, do otrzymanych włókien dodaje się lepiszcze. Może występować w postaci mat, płyt, otulin lub granulatu i może być łączona z innymi materiałami jak folia. Przewodność cieplna wełny szklanej wynosi 0.030-0.042 W/(m·K).
- Styropian – spieniony polistyren – otrzymywany poprzez spienienie litych granulek polistyrenu, zawierających rozpuszczony porofor (np. pentan). W zależności od stopnia spienienia uzyskuje się różne gęstości a od gęstości zależą właściwości izolacyjne; najlepsze są dla 25 kg/m3 do 33 kg/m3. Może występować w postaci płyt lub granulek. Przewodność cieplna styropianu wynosi 0.036 W/(m·K).
- Styrodur – polistyren ekstrudowany – otrzymany metodą ciągłej ekstruzji płyt (wytłaczanie przez głowicę szczelinową). Ma większą wytrzymałość mechaniczną i lepsze właściwości izolacyjne od styropianu. Do tego nie jest nasiąkliwy. Jest jednorodną pianą o komórkach w kształcie wielościanów, które do siebie ściśle przylegają. Przewodność cieplna styroduru wynosi 0.035 W/(m·K).
- Poliuretany – polimery zawierające grupę uretanową – powstające w wyniku addycyjnej polimeryzacji wielofunkcyjnych izocyjanianów (utwardzacz) z poliolami (żywica). Mogą mieć bardzo różne składy i właściwości. Głównie występują w postaci piany albo otwartokomórkowej albo zamkniętokomórkowej. Pierwsze występują w postaci piany o gąbczastej strukturze wypełnionej powietrzem z 90% otwartych komórek. Przewodność cieplna poliuretanów otwartokomórkowych wynosi 0.034 – 0.040 W/(m·K). Drugie są zamkniętymi pęcherzykami zawierającymi 90% gazów szlachetnych o lepszych właściwościach izolacyjnych i dużej odporności na zgniatanie.Przewodność cieplna poliuretanów zamknięto komórkowych wynosi 0.021 – 0.024 W/(m·K). Piany poliuretanowe są najczęściej stosowanym materiałem izolacyjnym w systemach GTT, Moss i LNT.
- Aerożele – sztywna piana składająca się w 90-99.8% z powietrza – powstające w wyniku stapiania idealnie czystej krzemionki w atmosferze nadkrytycznego dwutlenku węgla i rozdmuchiwanie jej za pomocą par rozpuszczalników organicznych poprzez stopniowe zmniejszanie ciśnienia. Stosuje się też metody chemiczne, polegające na reakcji skrajnie rozrzedzonych czterofunkcyjnych alkoksysilanów z parą wodną w atmosferze gazu obojętnego. Aerożele mogą powstawać na bazie różnych materiałów jak krzemionka, grafit, grafen, nanorurki węglowe, zeolity, aluminoksany, selenogermanidy czy cyjany platyny. Najlżejsze aerożele węglowe mają gęstość 0,16-0,18 mg/cm³ (1m³ waży 0.16kg), gdzie dla balsy było to 40 mg/cm³ Pomimo delikatnej budowy mają dobre właściwości mechaniczne i są odporne na ściskanie i rozciąganie. Przewodność cieplna aerożeli wynosi 0.017 W/(m·K).
- Nanoceramiczna powłoka termoizolacyjna – farba termoizolacyjna – jej podstawę stanowią próżniowe cząstki, zamknięte w ceramice stopionej w wysokich temperaturach i spojonej kauczukiem syntetycznym i innymi polimerami. W skład farby wchodzi styren i lateks akrylowy. Styren gwarantuje wytrzymałość mechaniczną a lateks akrylowy sprawia, że materiał ten jest odporny na warunki atmosferyczne i zapewnia odpowiednią elastyczność. Inne dodatki (biocydy, materiały przeciwporostowe i przeciwgrzybicze) sprawiają, że produkt jest trwały i odporny na pleśń. Właściwości izolacyjne bazują na zdolności próżni do ograniczenia przedostawania się chłodnego lub nagrzanego powietrza. Ogranicza ona możliwość stykania się ze sobą cząstek powietrza. Farba termoizolacyjna rozprasza 60-80% promieniowania podczerwonego. Efekt podobny jest do działania lustra. Producenci podają przewodność cieplną nawet rzędu 0.001 – 0.003 W/(m·K). Są to wartości poniżej zdolności pomiarowych i są mocno kwestionowane przez środowisko naukowe. Rzeczywiste mierzone wartości to 0.48 W/(m·K) i nie odbiegają od wartości zwykłych farb. Badania mikroskopowe nie potwierdziły też zawartości nanosfer, a raczej mikrokapsułek, które były do tego popękane, więc o żadnej próżni w nich zamkniętej nie może być mowy. Trzeba ten produkt traktować jako czysto marketingowy. W tym zestawieniu znalazły się tylko dlatego, że wiele źródeł w internecie zawiera informacje o niesamowitych właściwościach termoizolacyjnych farb nanoceramicznych/sfelolitowych umieszczając je w zestawieniu przewodności termicznej i opisując jako najbardziej izolacyjny obecnie znany materiał występujący w postaci ciekłej lub stałej.
Konstrukcje LNG wykorzystywane w praktyce
Prace nad konstrukcjami zbiorników i izolacji wciąż trwają. Część pojawia się tylko na desce kreślarskiej, czasem budowany jest prototyp lub seria statków, ale nie zdobywają one popularności lub pojawiają się trudności w eksploatacji. Spośród wszystkich możliwości na morzach można najczęściej spotkać następujące konstrukcje:
Moss (Kvaerner) - Rosenberg
Skonstruowany zgodnie ze standardem 2G, zbiornik niezależny typu B, kształtu sferycznego, do przewozu w pełni schłodzonego ładunku LNG.
Zbiornik jest samonośny, wykonany ze stopów aluminium lub 9% stali niklowej. Materiały te są rozszerzalne i kurczliwe termicznie. Zbiornik posiada pierścień, który pośrodku swojej wysokości jest podtrzymywany kadłubem wewnętrznym. Dzięki temu góra i dół zbiornika mogą się swobodnie rozszerzać.
Izolacja znajduje się na zewnątrz zbiornika i jest wykonana z piany poliuretanowej lub polistyrenowej. Najnowsze konstrukcje mają ratę parowania około 0.07% na dzień.
W izolacji znajdują się kanały wypełnione azotem jako gazem obojętnym. Przepisy pozwalają również na stosowanie suchego powietrza, pod warunkiem, że w przypadku wykrycia przecieku, przestrzenie te można szybko wypełnić gazem obojętnym.
Standardowo zbiornik może wytrzymywać ciśnienia 0.25 bara a maksymalna dopuszczalna wielkość to 0.7 bara.
Zbiornik wystaje znacznie ponad pokład i w górnej części nie wymaga bariery wtórnej. Ta jego część jest przykryta kopułą chroniącą zbiornik i izolację przed czynnikami zewnętrznymi. Natomiast pod zbiornikiem znajduje się dodatkowa, aluminiowa powłoka (taca) z płytami rozbryzgowymi. Chroni ona kadłub przed działaniem niskich temperatur w przypadku wycieku ładunku.
Są to jedne z najbardziej charakterystycznych konstrukcji, a zarazem najbardziej niezawodnych, trwałych i prostych w spawaniu i budowie.
Ich wadą są niewykorzystane przestrzenie wokół kulistego zbiornika.
Zdjęcia udostępnione dzięki uprzejmości Moss Maritime.
GTT (Gaztransport & Technigaz ) No96
Skonstruowany zgodnie ze standardem 2G, zbiornik membranowy, kształtu pryzmatycznego, do przewozu w pełni schłodzonego ładunku LNG.
Standardowo zbiornik może wytrzymywać ciśnienia 0.25 bara a maksymalna dopuszczalna wielkość to 0.7 bara.
Zbiornik nie jest samopodtrzymujący.
Pierwotna i wtórna membrana wykonana jest z inwaru (stop żelaza 64% i niklu 36% z niewielkim dodatkiem chromu). Materiał ma bardzo niską rozszerzalność i kurczliwość termiczną. Membrany są bardzo cienkie, zaledwie 0.7mm, oraz bardzo lekkie. Składają się z arkuszy o szerokości 500mm podtrzymywanych pierwotną i wtórną izolacją.
Membrana wtórna, identyczna jak pierwotna, jest wymogiem i zapewnia pełną ochronę konstrukcji statku przed uszkodzeniem w przypadku wycieku. Jednak w przypadku zaistnienia przecieku membrany pierwotnej na większej wysokości, podczas wyładunku istnieje potrzeba jej przebicia na dole, aby zbiornik się nie zapadł. Zbiorniki bez systemu podtrzymywania są podatne na efekt swobodnych powierzchni cieczy i wrażliwe na siły wywierane przez uderzający o jego ściany ładunek skroplonego gazu. Mają więc ograniczenia stanów załadowania. Z reguły zabronione są poziomy pomiędzy 10 i 70% wysokości zbiornika.
Rodzaj użytej izolacji, która za razem podtrzymuje zbiornik i oddziela go od kadłuba statku, zależy od wielkości i ciężaru zbiornika, wymagań właściciela oraz roku wykonania konstrukcji. System wciąż jest rozwijany i ulepszany. We wszystkich przypadkach grubość pozostała jednak taka sama; 230mm izolacji pomiędzy membranami i 300mm izolacji pomiędzy membraną wtórną i kadłubem.
– NO96 pierwotnie posiadał izolację z boksów wykonanych ze wzmacnianej sklejki wypełnionych perlitem. Rata parowania tej konstrukcji wynosiła 0.15%.
– NO96 GW perlit zastąpiono wełną szklaną. To pozwoliło zredukować ratę parowania do 0.125%
– NO96 L03 boksy dolne, za barierą wtórną, zmieniono na panele z piany i sklejki. W pozostałych miejscach pozostała sklejka i wełna mineralna. Rata odparowania została zredukowana do 0.11%
– NO96 L03+ zwiększono proporcje paneli ze sklejki i piany w stosunku do boksów ze sklejki i wełny. Rata odparowania zmalała do 0.10%
– NO96 Max posiada większą wytrzymałość mechaniczną przy zachowaniu niskiej raty odparowania. Membrany pozostały takie same, ale konstrukcja izolacji jest słupkowa i niestrukturalna, aby wytrzymywała większe naprężenia. Można ją również elastycznie modyfikować w zależności od potrzeb armatora i przewożonego ładunku.
– NO96 Super+ całkowicie zrezygnowano z boksów i paneli ze sklejki i zastąpiono je zarówno w pierwotnej jak i wtórnej izolacji płytami z piany poliuretanowej przekładanej płaskimi arkuszami wełny mineralnej. Współczynnik odparowania zmniejszono do 0.085%
Zaletami membrany są zdolności przewozowe w stosunku do zajmowanej powierzchni, lekkość, dobra izolacja, niska rozszerzalność termiczna.
Wadą jest delikatność konstrukcji i zabronione stany załadowania.
Zdjęcia udostępnione dzięki uprzejmości GTT France. Prawa autorskie Roland Mouron.
GTT (Gaztransport & Technigaz ) Mark III
Skonstruowany zgodnie ze standardem 2G, zbiornik membranowy, kształtu pryzmatycznego, do przewozu w pełni schłodzonego ładunku LNG.
Standardowo zbiornik może wytrzymywać ciśnienia 0.25 bara a maksymalna dopuszczalna wielkość to 0.7 bara.
Zbiornik nie jest samopodtrzymujący. Pierwotna membrana jest wykonana z pofalowanej stali nierdzewnej 304L o grubości 1.2mm. Dzięki fałdom stal może się rozszerzać i kurczyć.
Membrana ta podtrzymywana jest przez prefabrykowane panele izolacyjne wykonane ze wzmocnionej włóknem piany poliuretanowej o gęstości 130 kg/m3 i grubości 100mm.
Membrana wtórna wykonana jest z kompozytu, tak zwanego tripleksu. W jej środku jest folia aluminiowa a z jej obu stron przyklejony jest materiał z włókna szklanego. Występuje ona w dwóch wersjach; elastycznej FSB i sztywnej RSB.
Izolacja wtórna, znajdująca się pomiędzy wtórną membraną i kadłubem statku jest również wykonana ze wzmocnionej pianki poliuretanowej. Jednak jej grubość jest różna i decyduje o współczynniku parowania ładunku.
– Mark III – grubość izolacji wtórnej 170mm. Współczynnik parowania 0.150% – 0.125%.
– Mark III Flex – grubość izolacji wtórnej 300mm. Współczynnik odparowania 0.100% – 0.085%.
– Mark III Flex+ – grubość izolacji wtórnej 380mm. Współczynnik odparowania 0.070%
Zalety, wady i ograniczenia systemu GTT Mark III są podobne do GTT No96, gdyż obie konstrukcje są membranowe. Różnią się materiałem wykonania membran i izolacji je podtrzymujących.
Zdjęcia udostępnione dzięki uprzejmości GTT France. Prawa autorskie Roland Mouron.
LNT A-BOX
Skonstruowany zgodnie ze standardem 2G, zbiornik niezależny typu A, kształtu pryzmatycznego, do przewozu w pełni schłodzonego ładunku LNG.
Standardowo zbiornik może wytrzymywać ciśnienia 0.4 bara a maksymalna dopuszczalna wielkość to 0.7 bara.
Zbiornik jest samonośny. Posiada przegrodę wewnętrzną ograniczającą efekt swobodnych powierzchni cieczy oraz uderzania jej o ściany zbiornika (sloshing). Nie posiada żadnych ograniczeń stanów załadowania. Zbiornik jest bardzo wytrzymały i można w nim przewozić i cięższe ładunki aż do gęstości 0.6 t/m³. Może też wytrzymywać wyższe ciśnienia aż do 0.7 bara (im większy zbiornik tym maksymalne ciśnienie jest niższe). Minimalna temperatura nawet do -165ºC.
Zbiornik wykonany jest ze stali nierdzewnej lub 9% stali niklowej. Można go dowolnie formować w zależności od kształtu kadłuba. Jest on płaski, więc dobrze wykorzystuje dostępną przestrzeń.
Izolacja przytwierdzona jest do bariery wtórnej a nie do zbiornika głównego. Wykonana jest z pianki poliuretanowej. Jej grubość może być dowolnie regulowana w zależności od założonej raty parowania. Zwykle jest to 350 – 400mm.
Rata parowania w mniejszych konstrukcjach wynosi 0.15% – 0.20% ale dla dużych zbiorników już 0.075%.
Przestrzeń pomiędzy barierą pierwotną i wtórną jest dostępna do inspekcji.
Bariera wtórna jest wymagana przepisami dla ładunków o temperaturze poniżej -55ºC i jest również wykonana ze stali nierdzewnej. wkładana jest do kadłuba wewnętrznego, więc system ma układ pudełkowy.
Cały zbiornik może być wykonany poza stocznią, co ułatwia budowę statku. Statki w systemie A-Box może konstruować większa ilość stoczni. Przełamuje to hegemonię GTT, Moss oraz kilku wyspecjalizowanych miejsc budowy statków LNG.
W systemie A-Box można budować statki o dowolnej wielkości. Daje on możliwość szerokiego wykorzystania również na małych jednostkach operujących na mniejszych odległościach i docierających do miejsc ograniczonych głębokością akwenu. Stosuje się go też na bunkierkach LNG. Może być również wykorzystywany do przechowywania LNG jako paliwa na różnych typach statków. Daje także elastyczność przewożenia innych rodzajów ładunku np. etanu.
Wadą systemu A-Box jest ciężar konstrukcji, która jest wykonana z grubszej stali, oraz zawiera przegrody wewnętrzne. W systemie tym występuje jedna warstwa izolacji, ale gdy jest odpowiednio gruba, to można uzyskać raty parowania podobne do konstrukcji konkurencyjnych.
Zdjęcia udostępnione dzięki uprzejmości LNT Marine.